Automated Lidding for Nonwoven Wet Wipes: Robotic Solutions
The average consumer doesn’t give a second thought to how everyday consumer goods are packaged, especially simple boxes or sealed bags. Manufacturers of those goods, however, know that some products require rather complex packaging that, until recently, required assembly workers. One such example is nonwoven wet wipes packaged in a plastic bag with a flip-lid dispenser.
With a forecasted growth of 6.2% compound annual growth rate (CAGR), the wet wipe market is expected to be valued at more than $30 billion by 2029. To keep up with that growth requires advanced automation.
The Challenges of Automating Lidding Applications
While the packaging for nonwoven wet wipes isn’t complex, the assembly and robotics material handling process is. There are multiple steps to applying lids onto plastic wet wipe containers. Those individual steps are relatively simple, but putting all the pieces together within the desired tolerances and throughput rate is a major challenge.
Separate automation technologies must be perfectly aligned to perform multiple functions. For example:
- Conveyors move the customer product down the line into a cell, identifying the orientation of the products to ensure they are positioned correctly
- A dispenser presents lids to the robot and an adhesive applicator dispenses glue onto the lids at the designated rates and then affixes them to individual bags
- A quality control station inspects each product for potential defects as they move down the conveyor, triggering a tool that removes only defective pieces from the line
- Another case-packing robot picks and places the final products into boxes which are conveyed to a palletizing system
There are so many small details and nuances within each of these steps. Achieving all these functions with precision requires more than a capable robot; it requires expert engineering and programming skills. Programmers will perform custom coding using a programmable logic controller (PLC) that Interacts with the robot and other connected equipment. PLC is the brains of industrial machinery, controlling the conveyors, start/stop functions, buttons, photo eyes, and everything else interacting with it.
Tracking product locations in real-time to ensure correct placement is also complex. The programming must ensure:
- The lid conveyor has a lid in the correct spot at the right time
- The bag conveyor is moving at the desired speed
- The encoder is set up correctly to track products
- The correct amount of glue is administered
- The product is identified correctly
Solving the challenge of automating the wet wipe lidding process is all about the interaction between the robot and the PLC and getting all the communication and high-speed tasks working together. We aim for between 75–90 parts per minute, so each cycle of pick and place is less than a second. We can implement multiple robotic cells to multiply those results and deliver even higher ROI.
RELATED: 5 Complex Robotic Material Handling Trends & Challenges
Scaling a Wet Wipe Robotic Solution
Designing an automation system to achieve the task of wet wipe lidding is complex enough. But what if a production facility has multiple SKUs and product sizes, or updates the design of their lids or packaging?
We designed a dispenser that orients lids properly and our specially designed conveyor pulls each lid from the bottom of the stack. However, what if that lid has different orientations? We can determine the lid’s orientation and ensure the robot picks at the correct angle. When the lid reaches the pick position, it applies a new glue pattern and the robot aligns itself with the product’s angle to place it correctly.
Another challenge is that wet wipes often come in packs of 24, 48, 64, etc., each with different heights. The robot must be programmed to accommodate various dimensions.
Adjusting for these variations does not require new hardware, tooling, or conveyor adjustments. The robot can be programmed with different “recipes” for each product. An operator simply needs to toggle to the proper SKU on the menu interface. If new products are added after the robot’s installation, new SKUs can be programmed later.
Some producers have engineering staff that can handle reprogramming, but for others, our engineering staff at QComp Technologies can either visit or provide phone support to walk them through it. Because the entire robotic system uses the same code, the entire line stays in sync. Another advantage to using the same code throughout is in the event of a power outage, the code can be re-uploaded quickly from a backup, minimizing downtime.
An All-in-One System Streamlines Production
Robots can do a lot, but they are only one part of a solution. At QComp Technologies, we take a holistic and proactive approach to automation challenges, addressing the entire production line and making sure our solutions integrate seamlessly. For lidding applications, that means automating the process from the conveyor to the palletized product that’s ready for shipment.
Lid application is just one of the complex automation challenges we help solve. Check out several others in our guide, Robots Can Do That? 5 Complex Robotic Material Handling Trends & Challenges.
We invite you to connect with us to discuss how our team of experts can help you tackle your current automation challenges. Contact us today to explore the possibilities.
Share this
You May Also Like
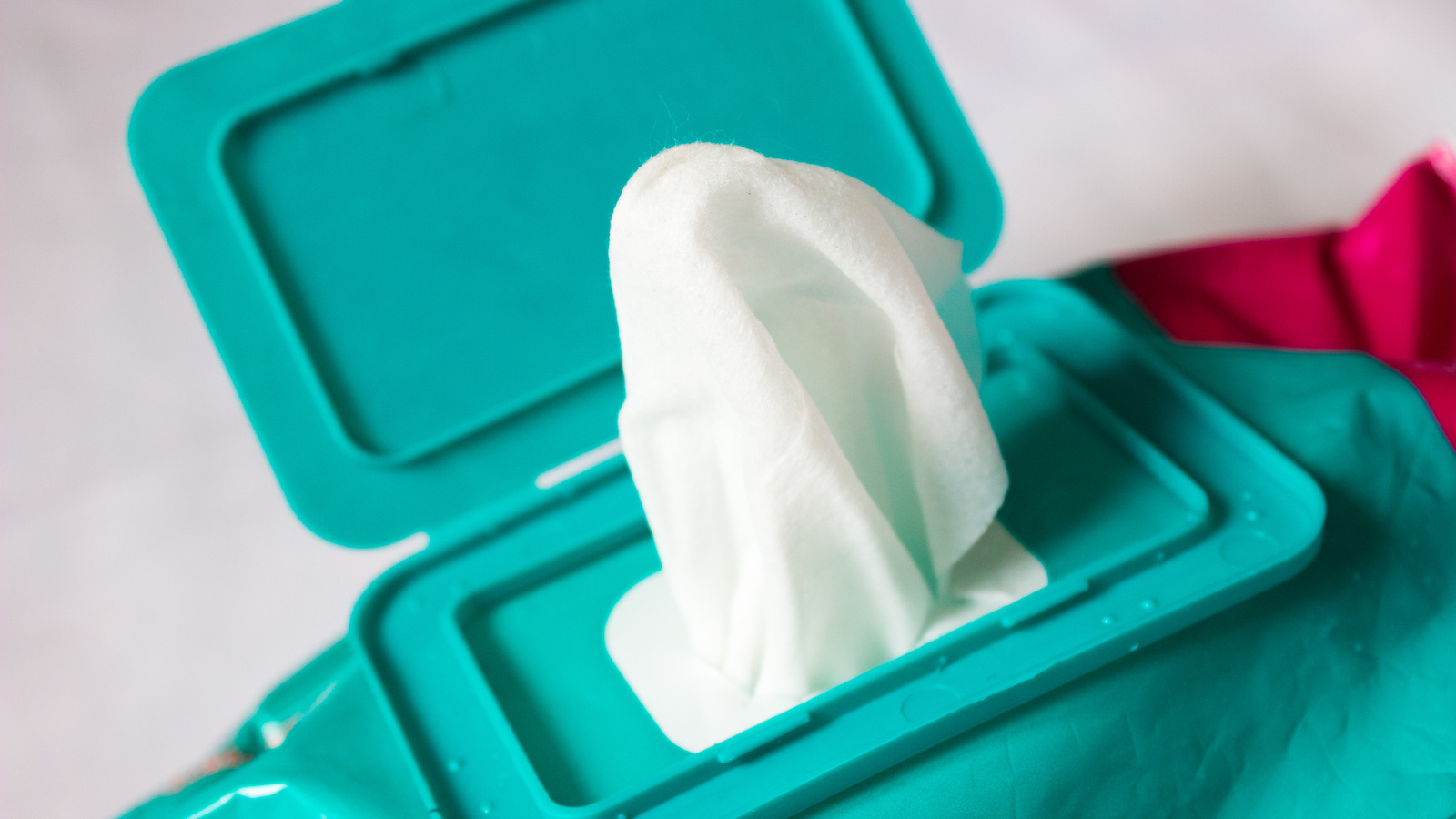
Wet Wipe Automation: Ensuring Scalable Robotic Solutions
Discover how scalable robotic automation adapts to varying nonwoven wet wipe packaging, ensuring accuracy, speed, and flexibility for manufacturers.
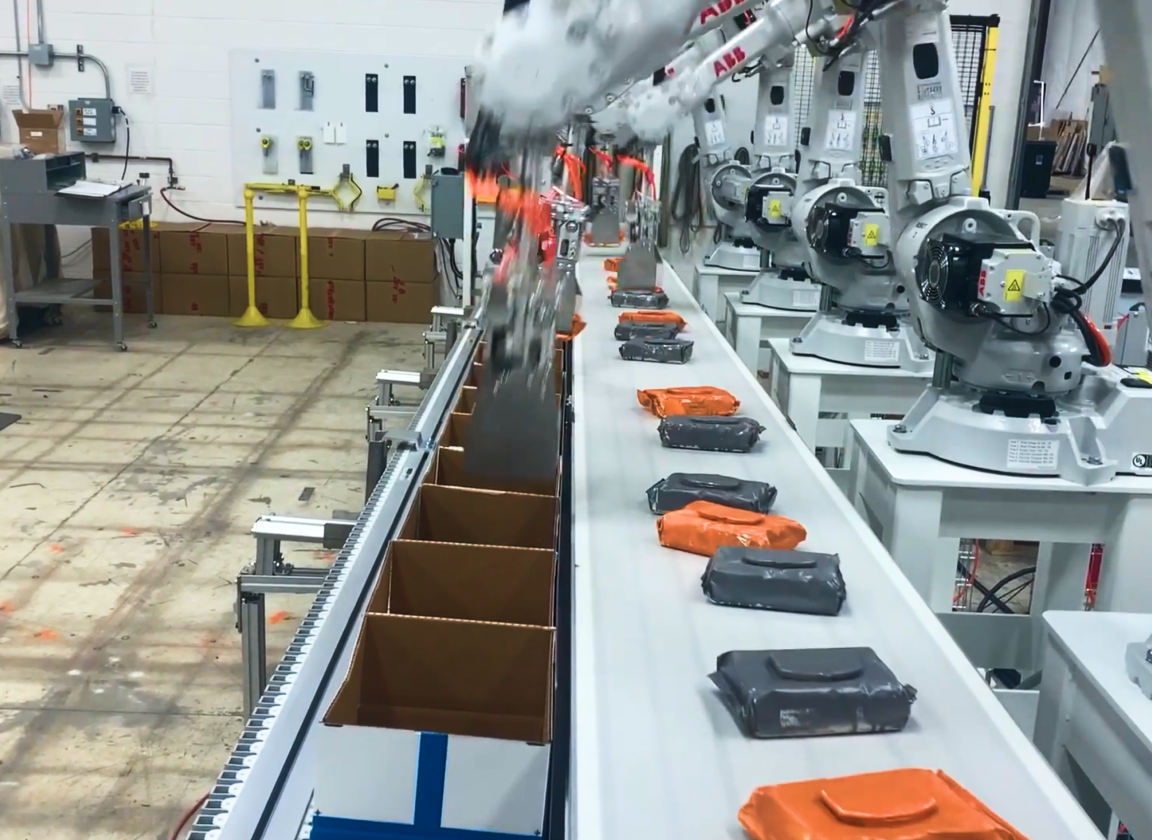
Robotic Automation ROI Analysis: Wet-Wipe Lidding Applications
Discover how robotic automation delivers ROI in the wet-wipes industry with cost savings, efficiency gains, and improved employee satisfaction.
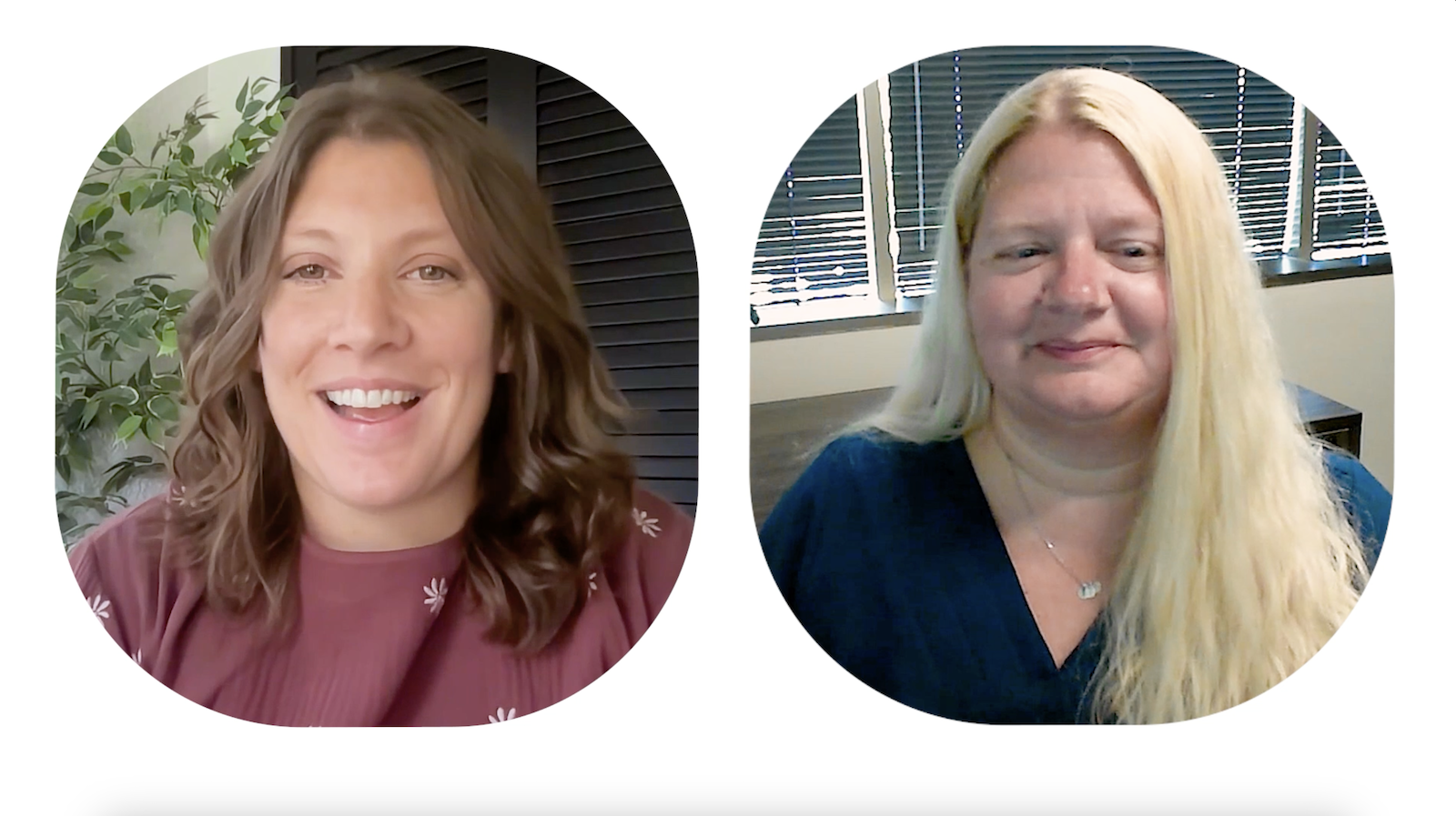
The Automation Advantage: Combat Labor Shortages and Win the Talent War
Discover how automation can help manufacturers tackle labor shortages, improve safety, and achieve a positive ROI in this insightful blog post conversation between industry experts.