The Automation Advantage: Combat Labor Shortages and Win the Talent War
In today's fast-paced manufacturing landscape, finding and retaining skilled labor has become one of the most significant challenges for businesses. With the labor shortage continuing to strain production lines, many manufacturers are turning to automation as a solution.
In our latest interview, we sit down with Katie Miner, Interim President, and Vice President of Technology at QComp, to explore how automation is not just filling the gaps but also enhancing safety, improving efficiency, and delivering a strong return on investment (ROI).
Transcript
SAMANTHA: I'm Samantha Himmelspach, Marketing Director here at QComp. Today, I'm speaking with Katie Miner, our Interim President and long-term Vice President of Technology. Good Morning Katie!
So today, we're going to be tackling one of the most pressing challenges facing manufacturers in decades: finding and retaining skilled labor. Katie, we all know manufacturers are struggling with the labor shortage, and we've had several companies approach us to see whether automation can help. What are you hearing from the manufacturers about the type of jobs that they've been having a hard time filling?
KATIE: That's a great question, Sam. Almost every opportunity that we see is a result of a manufacturer trying to automate a job, which they can't find anyone to complete. These jobs are often repetitive, potentially ergonomically challenging, and cause people to strain when completing them day in and day out. These jobs are typically a mix of skilled and unskilled labor, but the manufacturers are continuing to see changes in the workforce. Things like demographic shifts—there’s an aging workforce, and the entering workforce is smaller. There’s also this perception that jobs are seen as less attractive due to the physical demand, repetitive tasks, and working conditions. They often involve shift work, including nights and weekends, which is really just less appealing to potential workers today.
Unemployment continues to hover around 3-4%, but there is still a significant number of open positions. One report we saw last month listed more than 600,000 jobs open just in the manufacturing space in the United States alone. We've had a couple of recent examples where we spoke to some food manufacturers who are having issues keeping their production lines running due to staffing shortages. What they’re hearing is that the working conditions—the cold environment, physical constraints, and the monotonous nature of the work—are the key drivers of why they can’t fill these roles.
SAMANTHA: It’s interesting. I wonder why they haven’t thought about automating before.
KATIE: Automation in manufacturing is often surrounded by a lot of misconceptions that can influence how it's perceived, and really whether it’s implemented or not. One of the biggest misconceptions revolves around whether it will completely replace the human worker. The reality is that automation is aiming to augment labor, not replace it entirely. While certain repetitive and hazardous tasks may be automated, the human worker is still needed for complex decision-making, creativity, and problem-solving. Automation can lead to job displacement, but it also creates new opportunities in areas such as maintenance, programming, and oversight of automated systems. What we often find is that automation allows the upskilling of laborers in a meaningful way.
Another misconception is that automation is just too expensive and not worth the investment—it’s only for larger companies. Again, the reality is that the initial cost of automation can be significant, but the long-term benefits outweigh those expenses. Automation leads to increased efficiency, reduced labor costs, improved product quality, and enhanced safety, which results in a substantial return on investment over time. Typically, we see ROI happening within two to three years, depending on what is implemented.
The biggest misconception is they don’t think a robot can do what human hands can.
SAMANTHA: Interesting. Let’s unpack those a little bit. Do you think it’s true that there are some functions that robots can’t do, or has robotics advanced enough in recent years?
KATIE: That’s correct. Robots can’t do everything, but they can do a lot more than most people think. Many advancements in vision technology provide the inspection that a human operator would do as part of their process. Robots can provide force feedback, allowing for real-time adjustments, and also work collaboratively with humans.
QComp has designed several solutions providing high-speed picking of soft bags using vision systems to target the products. Specially designed end-of-arm tools allow the robots to pick the products at a high rate. Another application was the picking of food products. The system QComp installed provided visual inspection, looking for defects in the product while targeting the product to be picked, all while maintaining a higher rate of speed than a human worker can achieve.
QComp has also worked with several manufacturers handling glass to identify opportunities to automate, and all the advancements in robotics have allowed QComp to design solutions for picking large pieces of glass, keeping operators out of harm’s way, safe from potential injuries, while also inspecting for defects.
New technologies and the various experiences that an integrator like QComp has may look at automation as a challenge from a different perspective. We encourage all manufacturers to explore automation solutions, even if they’ve been told in the past that it’s not possible. Continued technological advances are eliminating those barriers to entry.
SAMANTHA: Interesting. I’m going to go back to something you mentioned earlier. So it’s not just about finding workers—it’s about protecting worker safety too?
KATIE: Absolutely. Automation can significantly enhance safety in manufacturing environments by reducing the risk of human error, minimizing exposure to hazardous conditions, and improving overall workplace safety protocols. In the example I shared in the glass manufacturing space, those units are heavy and cumbersome, often weighing hundreds of pounds to sometimes over half a ton. Many of the systems we’ve installed helped improve quality by more precisely handling a large piece of glass, rather than manually having a piece of equipment and an operator do it. Robotically handling these pieces not only removes the employee from the heavy lifting, it keeps them out of harm’s way should a panel of glass crack.
Another automation system we implemented involved operators placing bags of ingredients into a cup, doing this 60 to 70 times per minute. The operators had to rotate with others on the line every 15 minutes, as their hands would cramp up from repetitively pushing the bag into the cup. A system was installed to perform this function, doing it all day long, not only increasing the line throughput but also solving one of their hardest roles to fill.
Automation significantly enhances workplace safety because it reduces human error, minimizes exposure to hazardous conditions, improves ergonomics, and ensures consistent safety compliance throughout the building. The integration of advanced safety features, real-time monitoring, and predictive maintenance further contributes to a safer work environment. By automating dangerous and repetitive tasks, manufacturers can protect their workers and create a safer, more efficient workplace.
QComp is an A3-certified robotic integrator. That certification is centered around the safety of the cell and the operator surrounding it. The certification adheres to OSHA, ANSI, and ISO safety standards, and the high level of emphasis on the cell is met, as well as the many ergonomic benefits of automating repetitive and dangerous material handling operations. This helps manufacturers reassign employees to higher-value tasks within the organization.
SAMANTHA: Perfect. Those are wonderful examples. Thank you. I am going to have us pivot and go back to something we kind of talked about earlier, which is cost. I think every manufacturer wants proof that a robotic integration will not only help them ease the labor shortage, but will also deliver a positive ROI. What are your thoughts on that?
KATIE: Yeah, assessing the ROI is the most important thing that needs to happen for a manufacturer, and it’s essential for making an informed decision. By providing a clear and quantifiable measure of the benefits versus the cost, the ROI analysis supports manufacturers in achieving sustainable growth and operational efficiency. It really can make sure that their competitive advantage in the marketplace is maintained. An ideal ROI would see this happen in 24 months, but it may vary case by case, depending on all factors.
The ROI will not only look at the initial investment costs, but will also incorporate operational cost savings such as labor savings, increased production, an ability to have a greater standard of quality, and some of those indirect benefits such as safety and employee satisfaction, as well as the ability to scale the business based on that automation.
One automation cell we implemented at a food manufacturer was able to relocate two roles on a line by installing two robots. This was across three shifts a day. The salary and benefits are factors, but there are other tangible and intangible benefits, like increased productivity. Because robots can run at faster rates, they don’t need to take breaks, and there’s no shift change. This also ensures employee satisfaction increases, and you have reduced turnover rates as these are all key measures you should be looking at.
SAMANTHA: What are the first steps a company should take when they’re looking to explore whether automation might be a solution for their labor shortage? What does that process look like?
KATIE: Well, the first step to exploring automation would be to reach out to QComp. A team will provide a site visit, walk the facility, and do a cursory audit of the operations. They will help to identify potential areas for automation that will make an impact. We work hand in hand with our customers to identify pain points and key areas where automation may be a great fit. If you’re new to automation or you already have ideas of what your company may need, QComp will work with you to ensure the best solution is provided. QComp can also provide prototypes and demonstrations to help mitigate areas of concern within a particular application. This helps to visualize what the future may look like in your facility.
SAMANTHA: Wonderful. Well, thank you, Katie. This has been incredibly informative and thanks again to those who are watching. And just a reminder, if you want to explore how automation can help your organization tackle labor shortage, improve safety, and deliver the results you need, get a hold of us here at QComp by clicking Let’s Connect in the right-hand corner. Thanks everyone!
Share this
You May Also Like
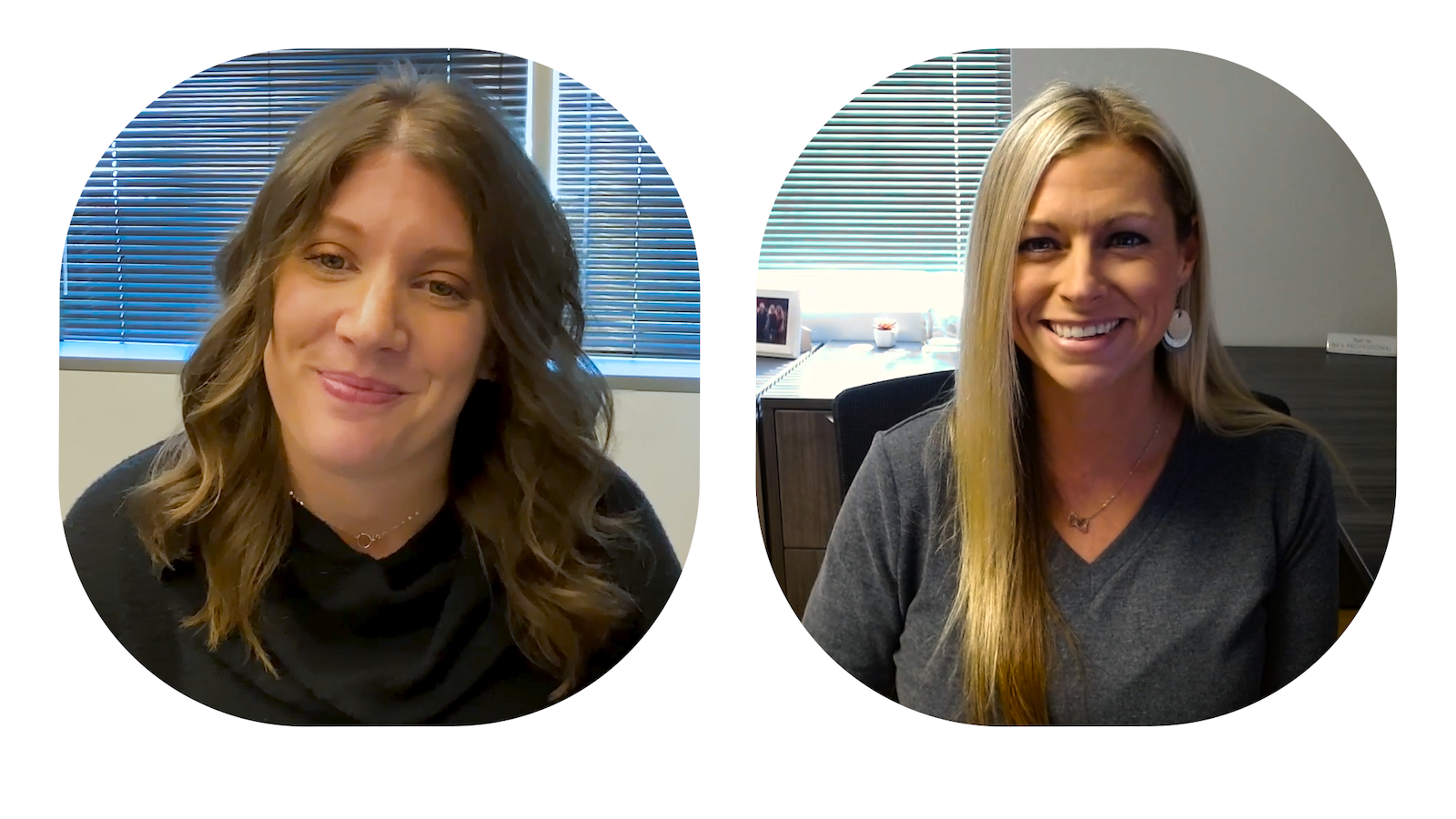
How Customized Automation Delivers High ROI
Discover how robotic automation drives ROI, improves productivity, and addresses labor challenges in this insightful conversation with QComp experts.
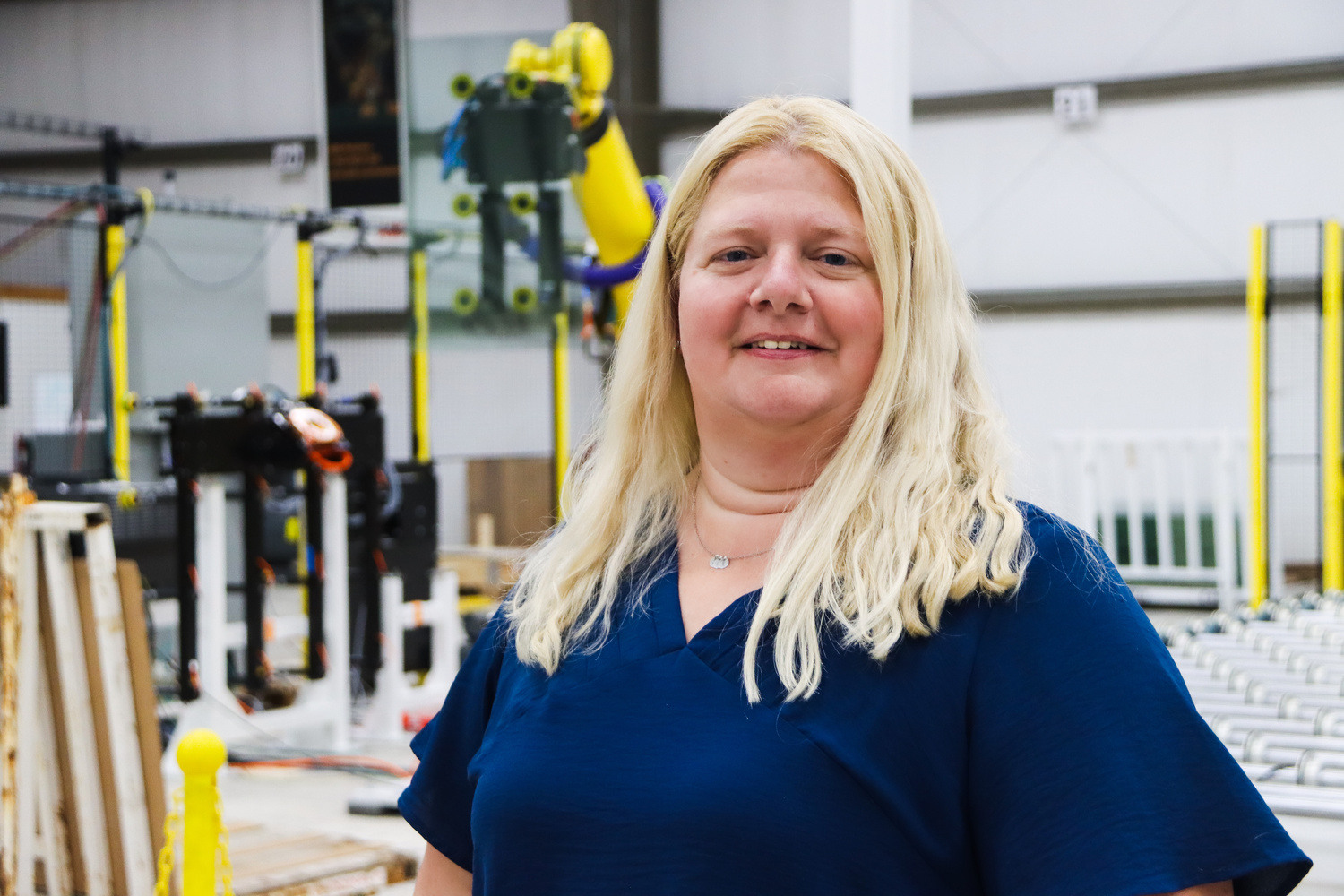
QComp Technologies Announces Company President
Katie Miner is named president of QComp Technologies, bringing expertise to lead the employee-owned company in innovative robotic solutions for complex industries.
-1.jpg?width=1500&height=1000&name=Katie-Miner-QComp%20(2)-1.jpg)
Leading the Charge: An Interview with Katie Miner
Katie Miner of QComp Technologies discusses robotic systems, her career journey, and the future of robotics in manufacturing on the NEW Manufacturing Insights Podcast.